© 2024 MJH Life Sciences and Pharmaceutical Technology. All rights reserved.
© 2024 MJH Life Sciences™ and Pharmaceutical Technology. All rights reserved. Product Inspection Sheet
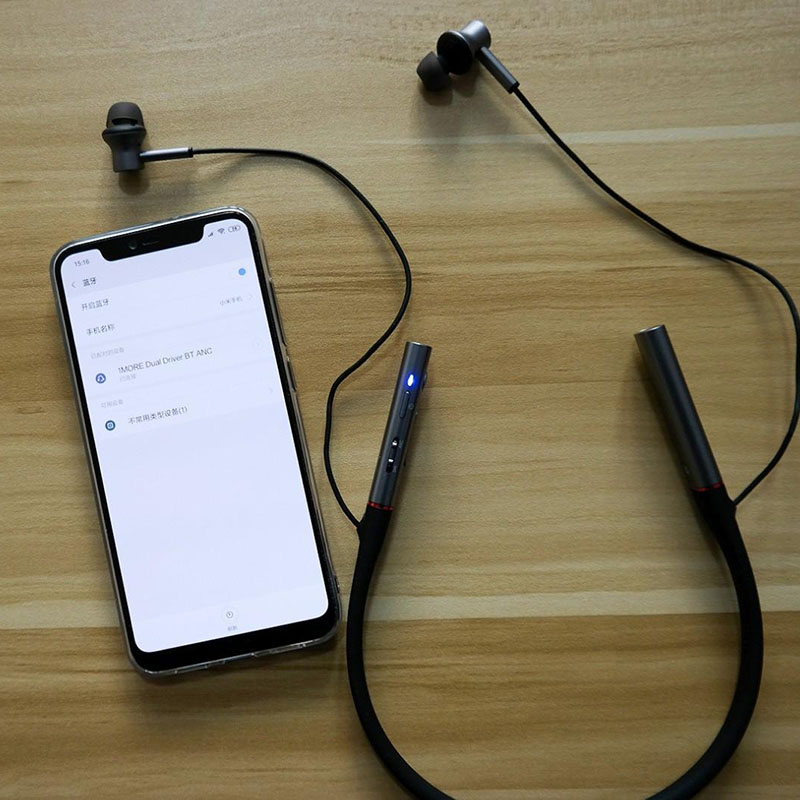
Final product inspection results should be included as part of the batch release documentation, says Susan J. Schniepp, distinguished fellow at Nelson Laboratories, LLC.
Q: My company is a contract manufacturer. Our final product inspection process consistently delays timely release of the manufactured products to our clients. Is there a best process/practice for performing final product inspection?
A: This is not a new problem for the industry. To me, some of the issue is the fact that we call the specific activity of the overall physical product evaluation the “final product inspection.” In my opinion, the physical product evaluation should start at the beginning: the receipt of the individual components (stoppers, vials, labels, etc.) that are used in manufacturing. Each component should pass an incoming quality inspection with defined acceptable quality limits (AQL) and clear directions for rejection of the component should it exceed the AQL. The specific elements to be looked at on incoming inspection will vary depending on the component.
Let’s assume your company manufactures sterile injectable products and the major component you will use in manufacturing is a glass vial. The first step in the process is to perform an incoming inspection of the glass vials. The number of vials to inspect from the shipment will depend on the number of vials contained in the shipment. The sample size to be inspected should be recorded in the appropriate standard operating procedure (SOP). The specific defects to be inspected should also be included in the SOP. When evaluating these defects, most companies employ definitions of critical, major, and minor to the reject/accept criteria. In the case of vials, critical might be defined as likely to cause harm to the patient; major might be defined as leads to impairment to the patient; and minor would be defined as cosmetic defect causing no threat to the patient. Defining the acceptance criteria upfront may save you a lot of time at the end of the process.
Once the vial is accepted, it will be used in the manufacturing process. Defects that exist in the vial after initial acceptance may be detected during this step of the process. Many manufacturing lines have automatic sensors that detect vial imperfections and eliminate the vial from the batch before it is sent for labeling. It is important for the line operators to be trained to recognize when there is an increase in rejected vials because this could mean that the incoming inspection did not pick up the vial defect. Again, if the defect can be detected and categorized at this process stage, it will save time at the product release stage.
The last stage for potential vial inspection before labeling would be visual inspection of the stoppered vial. Some companies perform this step manually with trained visual inspectors while others utilize visual inspection equipment to perform the final inspection of the vial before labeling. Companies using vial inspectors typically focus those inspectors on looking for particulates in the vial, but they should also be trained to recognize vial defects. Regardless of which inspection format is used, there should be SOPs and AQLs governing the inspection process.
Final product inspection results should be included as part of your batch release documentation, so it is important to have repeatable, defined process/processes in place at all stages of the manufacturing process that is/are suitable for the product being inspected. The more time you spend upfront in the component inspection process, the more efficient your final inspection and batch release process will be to ensure timely product release to your clients.
Susan J. Schniepp is distinguished fellow at Nelson Laboratories, LLC.
Pharmaceutical Technology Vol. 47, No. 12 December 2023 Page: 34

General Cargo Inspection When referring to this article, please cite it as Schniepp, S. Final Product Inspection: Making the Most of Your Processes. Pharmaceutical Technology 2023 47 (12).