Turning Facility Data Into Bottomline Benefits » The First 100 Days as a Facility Manager » 2023 Vision Award Winners » Staffing Strategies from Recruitment to Retention »
When a premium retailer was looking to strengthen their safety program, Master Lock delivered. Chosen for their proven track record and highly collaborative approach, Master Lock thought outside the box to develop a unique set of custom solutions that kept this retailer complaint and their employees safe. Lockout Locks
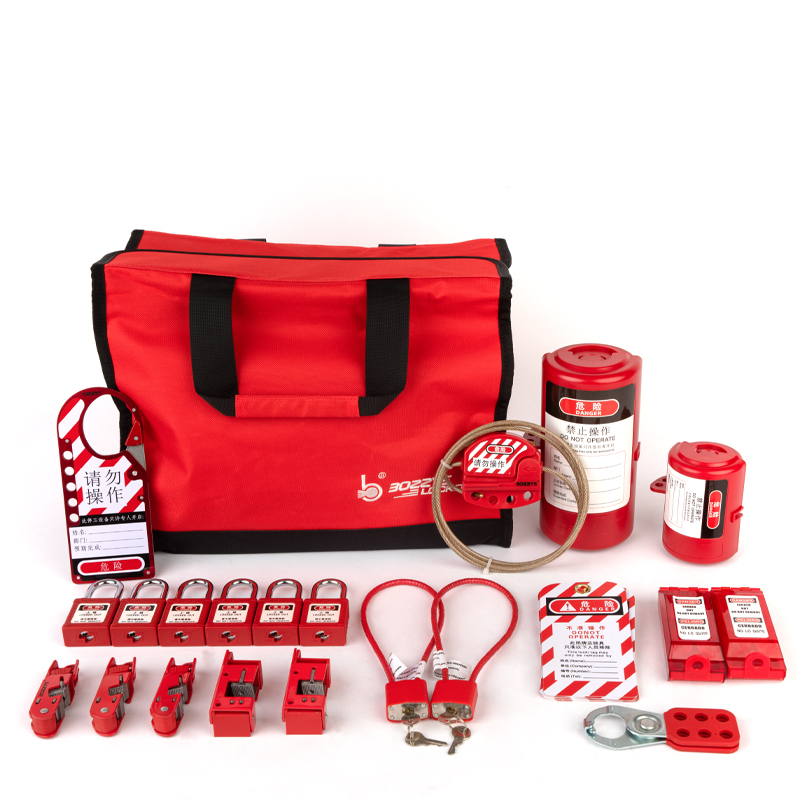
A large, multi-site retailer needed professional assistance in writing lockout procedures for their machinery and equipment at over 450 stores across multiple states. Their end goal was compliance and safety during the servicing and maintenance of their equipment. Given their unique challenges that required out-of-the-box thinking, Master Lock was the clear choice based on their experience, expertise, flexibility, and creative problem solving when developing individualized plans and scopes of work.
As an organization highly committed to safety, it was important to this premium retailer that they take a proactive approach to control any hazardous energy that could impact safety and/or the efficiency of their stores — and the sooner the better. It was also important to ensure that the customer shopping experience was not interrupted in any way.
One unusual and daunting challenge they faced was identifying the power source for each piece of equipment in every store to create a usable outline that accurately mapped each location’s electrical system. And with three different store configurations, it was critical to develop a unique approach. A “one size fits all” solution wasn’t going to work here.
In addition to the mapping, the retailer made it a priority to have equipment-specific lockout procedures created for each of the hundreds of pieces of equipment in each store. Access to the procedures was an important component to ensure they were readily available to their entire team of internal authorized personnel in charge of servicing and maintaining the equipment. With frequent engagements with outside contractors, they also needed to be able to easily communicate the organization’s hazardous energy isolation methodology to contractors using these new equipment-specific lockout procedures.
They knew that the electrical mapping as well as the new policies and procedures were critical to keeping everyone – from internal employees to contractors – accountable for adhering to the organization’s safe work commitment, without causing any unnecessary downtime in the stores. And they chose Master Lock to help.
With frequent engagements with contractors, the client had 5 key goals related to their lockout procedures:
After presenting and discussing multiple options with varying degrees of involvement of Master Lock and the customer, it was determined that Master Lock would write all lockout procedures, including supporting materials, provide software with training, and conduct electrical mapping for each store.
With open minds and a nimble approach, Master Lock was able to collaboratively discuss the client’s challenges and create flexible solutions that met their unique needs in accordance with their budget and timeframe. After each store was completed, it was clear what steps needed to be taken to de-energize equipment using the appropriate circuit breakers and disconnect identified in the electrical system mapping.
With approximately 25% of the stores complete, the client was able to see immediate results supporting their goals of compliance, safety, accountability, procedure updates and mapping.
To contact a Master Lock safety specialist to discuss ways we can partner with you, visit https://www.masterlock.com/lockout-tagout-solutions/professional-safety-services?business#safety-contact

Adjustable Valve Lockout Download the full PDF of this case study at insights.masterlock.com/articles/optimizing-lockout-procedures-for-a-multi-site-national-retailer