The vision for superior castings and customer service dates back to May 1963 when Joe Peers, who had been in the foundry industry all his life, founded his own foundry manufacturing malleable iron castings. For most of this period there has been a family connection of Joe’s in the company with son-in-law Ben Dyson having worked for the company from 1963 until retiring in 2006 and grandson, also christened Ben, has been with the company as Managing Director since 2011.
Joe Peers was born in England and educated at Sutton-in-Ashfield High School and Mansfield Technical College. His involvement with the malleable iron casting industry began in 1930, in which year he joined Ley’s Malleable Castings Company Limited in the UK. Melting And Pouring Auxiliary Equipment

The casting platform with 10 moulding lines and two pouring lines
In 1947 he took up an appointment in South Africa and in 1950 founded J. C. Malleable (Pty) Limited, South Africa. He later became works manager of African Malleable Foundries Limited, leaving them in 1963 to start Malleable Castings.
Joe Peers was a member of the British Institute of Foundrymen and joined the South African Institute of Foundrymen when he arrived in South Africa. He would go on to be elected President of the SAIF and remained an active member during his working career.
The history of the company shows that Joe Peers sold the company to General Mining in the 1970s and remained on as a consultant. The company was then sold to Malbak Limited and then this Group sold it on to EC Lennings, a foundry group with a long history in South Africa.
In 1992 two private investors, Mike Jolly and Terry Burgess, took ownership and they are still the current owners.
Zimmerman jolt squeeze moulding machines
Prevailing CEO and a shareholder Joe Fletcher joined the company in 1989 as General Manager and he was subsequently promoted to the position of MD/CEO when Mike Jolly and Terry Burgess took ownership.
Affable Joe takes up the story. “I have been with the company for virtually half its existence. In that time I have seen changes in both the company and the industry. At one time the company even operated a cupola furnace but thank goodness we have moved with the times and installed induction furnaces, with our latest one installed earlier this year.”
Change from malleable iron production to SG or ductile iron production
“The biggest change in the company came when we made the decision to change from manufacturing malleable iron castings to SG or ductile iron castings in 2005.”
“The company was founded on the production of malleable iron castings and today malleable iron is still widely used in industry. At the time it was the preferred material of use as ductile iron was relatively new for foundries as it had only been introduced in 1948, and would only become recognised and commercially viable much later.”
MD Ben Dyson, CEO Joe Fletcher and Foundry Manager Pradeep Singh
“Malleable iron is cast as white iron, the structure being a metastable carbide in a pearlitic matrix. Through an annealing heat treatment, the brittle structure as first cast, is transformed into the malleable form. Carbon agglomerates into small roughly spherical aggregates of graphite leaving a matrix of ferrite or pearlite according to the exact heat treat used. Three basic types of malleable iron are recognised within the casting industry: Blackheart malleable iron, Whiteheart malleable iron and Pearlitic malleable iron.”
“It has greater ductility than grey cast iron for example, because of its carbon content (2.5wt %), silicon content (1.0wt %), and manganese content.”
“Malleable cast irons may often be used in place of steel at considerable cost savings. The design and production advantages of malleable cast iron include low tooling, and production cost, good machinability without burring and also the ability to cast into complex shapes. But the microstructure and mechanical properties of malleable cast iron is affected by factors such as chemical composition of the iron, rate of annealing and also the type of graphite formed (if any).”
“Ductile cast iron, previously known as nodular iron or spheroidal-graphite (SG) cast iron (the international term is ductile iron), is cast iron in which the graphite is present as tiny spheres (nodules). In ductile iron, eutectic graphite separates from the molten iron during solidification in a manner similar to that in which eutectic graphite separates in grey cast iron.”
Casting sizes and weights range from 0.1 kilogram to 30 kilograms, shell cores are produced in-house to satisfy the full range of castings produced and the pattern plate dimensions are 460mm x 160mm and 500mm x 160mm
“However, because of additives introduced in the molten iron before casting, the graphite grows as spheres, rather than as flakes of any of the forms characteristic of grey iron. Cast iron containing spheroidal graphite is much stronger and has higher elongation than grey iron or malleable iron. It may be considered as a natural composite in which the spheroidal graphite imparts unique properties to ductile iron.”
“The relatively high strength and toughness of ductile iron give it an advantage over gray iron or malleable iron in many structural applications. Also, because ductile iron does not require heat treatment to produce graphite nodules (as does malleable iron to produce temper-carbon nodules), it can compete with malleable iron even though it requires a treatment and inoculation process.”
“The mould yield is normally higher than with malleable iron. Ductile iron can be produced to x-ray standards because porosity stays in the thermal center. Malleable iron cannot tolerate porosity because voids migrate to the surface of hot spots such as fillets and appears as cracks. Typically, the composition of unalloyed ductile iron differs from that of grey iron or malleable iron.”
Spud type castings post knock off and ready for fettling
“The raw materials used for ductile iron must be of higher purity. All cast irons can be melted in cupolas, electric arc furnaces, or induction furnaces. Ductile iron, as a liquid, has high fluidity, excellent castability, but high surface tension. The sands and moulding equipment used for ductile iron must provide rigid moulds of high density and good heat transfer. The formation of graphite during solidification causes an attendant increase in volume, which can counteract the loss in volume due to the liquid-to-solid phase change in the metallic constituent.”
“Ductile iron castings typically require only minimal use of risers. Grey irons often do not require risers to ensure shrinkage-free castings. On the other hand, steels and malleable iron generally require heavy risering. Thus, the mould yield of ductile iron castings (the ratio of the weight of usable castings to the weight of metal poured) is much higher than that of either steel castings or malleable iron castings, but not as high as that of grey iron.”
“There are some cases of ductile iron castings being made without risers. Often designers must compensate for the shrinkage of cast iron during both solidification and subsequent cooling to room temperature by making patterns with dimensions larger than those desired in the finished castings. Typically, ductile iron requires less compensation than any other cast ferrous metal. The allowances in patternmaker rules (shrink rules) are usually: Shrinkage allowance can vary somewhat from the percentages given above, and often different percentages must be used for different directions in one casting because of the influence of the solidification pattern on the amount of contraction that takes place in different directions. Shrinkage is volumetric, and the ratio of dimensions to volume influences each dimension. As ductile iron approaches a condition of shrinkage porosity, the graphite nodules tend to become aligned and can result in lower fatigue strength.”
A valve body casting with internal section done with shell core
“During recent years, producers and users of ductile iron castings have observed that many potential users of ductile iron castings are not aware of the wide range of properties offered by the family of ductile iron alloys.”
“Since their commercial introduction ductile iron castings have proven to be a cost effective alternative to malleable iron castings, steel castings, forgings, and fabrications. This is for a multitude of reasons and ductile iron castings are found in every field of engineering and in every geographic area of the world.”
“Ductile cast irons are used extensively in automotive applications such as clutches, gears, carriers, shafts, bearings, cams and hubs. Castings are made in a wide range of sizes with sections that can be either very thin or very thick.”
“Since its introduction, the growth of ductile iron applications has exceeded all expectations. Whether in an automobile component, a water pipe, or a plow, ductile iron has made major inroads to the casting market in every industrially developed country. There can be little doubt that the major motivating factor for this was “more strength for less expense” compared to just about every other cast alloy. The lesser expense comes not only from the readily available raw materials and the efficiencies of the foundry operation, but also from reduced cleaning and machining costs of ductile iron castings. The application of ductile iron is a notable engineering achievement of our age.”
Markets supplied include mining, overhead line, agriculture, small tools, building and scaffolding, railway and automotive
“In our case it was not only the reasons given above but a case of us becoming more competitive in the market place as well. With the influx of all the castings from China, our decision has been vilified.”
New Solid State 1.5 megawatt furnace
“When I joined the company at the beginning of 2011 one of my briefs was to look at all areas of the foundry and come up with solutions to improve our productivity, improve quality, reduce costs and scrap rates” said MD Ben Dyson. Ben completed a four year apprenticeship with Malleable Castings doing training at Iscor, then worked at Eclipse East Plant, followed by a few years in the control and automation industry before then serving as the Managing director designate for a well-known induction furnace manufacturer where he was exposed to European training and international and local installations.
“It was kind of dejavu for me joining Malleable Castings. With all the family history I felt as though I was ‘coming home’. It was an opportunity I could not miss.”
The new Solid State 1.5 megawatt medium frequency furnace was installed earlier this year
“The foundry has operated from the same location since my grandfather purchased the land in 1961 and started the foundry in 1963. There have been additions and changes to buildings but basically the foundry has operated as a green sand foundry since the beginning. The company did make some major equipment purchases in the 80s and we still have most of this equipment operating today. This includes the Richards mill/mixer, a Speedmullor 75B and the eight Zimmermann jolt squeezing machines with match plates.”
“In total we have 10 moulding machines and we are turning over in the region of 340 boxes a day per machine. We have regularly serviced and maintained this equipment and the machines still operate as though they are new, although we are looking seriously at purchasing a fully automated moulding machine.”
“However I did have to look at our melting capacity. When I joined we had an 8 ton furnace, with a Crescenzi power pack and BBC ITMK5 cradle and two Lowenstein 3 ton furnaces, all of which are power hungry, especially during holding when not running production, which is one of the disadvantages of mains frequency furnaces. The arrival of the new Solid State 1.5 megawatt medium frequency furnace earlier this year could not have come sooner. To accommodate the new furnace we removed one 3 ton mains frequency furnace. I also introduced gas pre-heating of the scrap and this is making a difference. I constantly monitor our power usage online and make every effort to be wise during the peak periods, especially on winter tariffs. The other important factor in using furnaces efficiently is good quality scrap and good charging practice. And of course the golden rule, keep the lid closed on your furnaces. Our production is now up and we are saving on our power consumption.”
“We are very proud that our returns from customers are down to less than one percent and our scrap rate has been reduced down to between six and seven percent. This is a big improvement and we are constantly working on this.”
“The quality of our metal is of top priority and here we utilise a Spectro spectrometer, which is housed in a climate controlled laboratory.”
“Our other big challenge is patternmaking. I constantly investigate new methods of tool making. If we have a CAD drawing from our customer this is first prize but we now utilise the new technologies available, from CAD/CAM cutting to 3D printing of masters. We maintain all our own patterns.”
Founder Joe Peers was a member of the British Institute of Foundrymen and joined the South African Institute of Foundrymen when he arrived in South Africa. He would go on to be elected President of the SAIF and remained an active member during his working career
“The fettling area is in a separate building with the heat treatment furnaces, shot blasting and dispatch. The process flow is overall very efficient throughout the facility.”
“Our casting sizes and weights range from 0.1 kilogram to 30 kilograms, shell cores are produced in-house to satisfy the full range of castings produced and our pattern plate dimensions are 460mm x 160mm and 500mm x 160mm.”
“Markets supplied include mining, overhead line, agriculture, small tools, building and scaffolding, railway and automotive. Malleable Castings is a flexible foundry capable of producing cost effectively, both long production runs and shorter, lower volume orders to satisfy the full range of customer needs.”
“We specialise in the production of relatively small parts, with tight tolerances, excellent machining characteristics and very good surface finish. On request we can have the castings painted, galvanised or electro plated.”
A burner body that required many trials before the company succeeded in manufacturing a casting to the client’s satisfaction. One of the difficulties was due to the escape of gas from the core. The company’s motto is that they rather try and maybe fail than fail to try
“As standard practice we work closely with our customers to assess critically and then develop the optimum pattern and feeder system for each casting so as to build in from the start the lowest scrap rates and greatest cost efficiencies.”
This is a new area that Malleable Castings has recently ventured into. “We have had requests from clients so we are starting off small and we will see how we go. We have the space so that is not a problem,” said Joe Fletcher.
The company currently employs 120 staff with over 75% that have worked for Malleable Castings in excess of 15 years. The current capacity is 200 tons a month and presently it is casting up to 140 tons a month.
For further details contact Malleable Castings on TEL: +27 (11) 822 1503 or visit www.malleable.co.za
The quality of the metal is of top priority at Malleable Castings and here they utilise a Spectro spectrometer, which is housed in a climate controlled laboratory
Furane sand mould before coating and closing
A new project for a cooling jacket
All shell cores are produced in house on 14 shell core machines
Shell cores for the internal thread of a product. After casting the thread never requires any further work
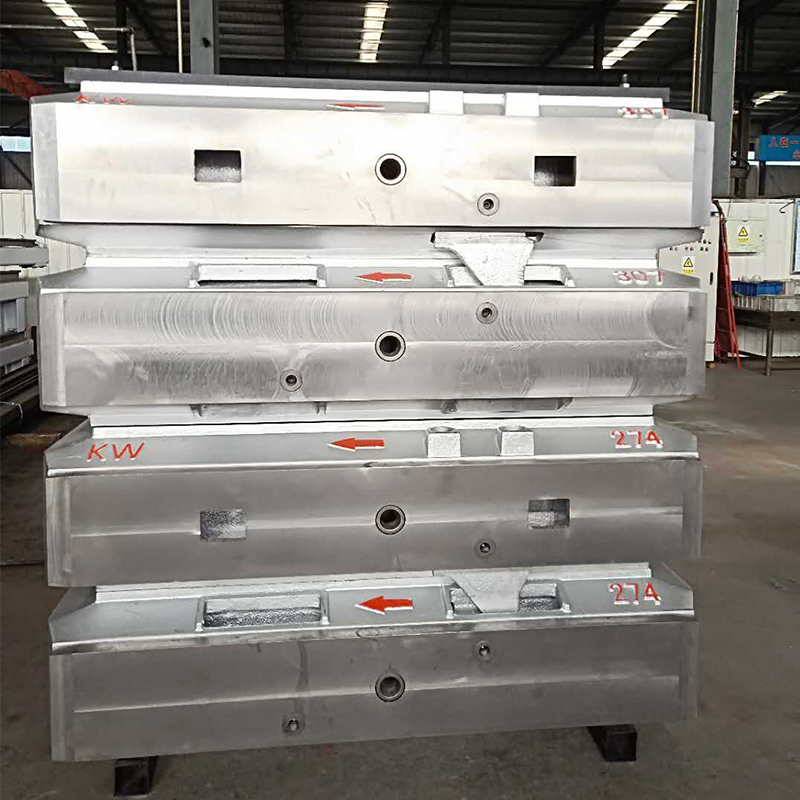
Moulding Machine 150 Kg ladles being preheated for the next tap